At the core of cleaner, smarter agglomeration.
Bridging Materials and Markets
Backed by more than 20 years developing green pellets and briquettes for the mining and steel industries, Coldbound Technologies transforms underutilized raw materials and industrial waste into high-value, sustainable agglomerates, aligning technical performance with market demand.
More than 100 unique formulations developed through applied research and industrial testing.
Accelerating Industrial Decarbonization
Through tailored project assessment, process design, in-depth validation, and ESG advisory, Coldbound Technologies helps clients reduce emissions, comply with evolving regulations, and unlock new revenue streams. By applying the most advanced cold agglomeration technologies, we produce furnace-grade pellets and briquettes with minimal environmental impact.
Reductions of up to 80% CO₂e.
Near-zero NOx and SOx.
Energy consumption as low as 12 kWh per tonne of pellet.
De-risking Technology Adoption
From lab to plant, we provide end-to-end support—from material characterization to commissioning—ensuring reliable scale-up and faster return on investment. Our approach ensures smooth scale-up, operational reliability, and a faster return on investment, empowering clients to adopt cold agglomeration with confidence and clarity.
Up to 90% lower CAPEX.
Comparable OPEX.
Fastest ROI in the market.
Process Integration
Binding Systems

We specialize in seamlessly integrating a variety of binders, ensuring that each solution is optimized for material type and end-use application. Our expertise bridges the gap between raw material characteristics and finished product quality, driving superior performance in each step of the cold agglomeration process. Achieving successful integration—both technically and economically—requires careful balancing of a wide range of chemical components.
- Organic Binders.
- Inorganic Binders.
- Specialized Additives.
Dedicated Equipment

We combine deep expertise in binder chemistry with advanced agglomeration technologies to deliver optimized solutions. By carefully selecting and integrating the right binding systems with dedicated equipment, we ensure superior pellet and briquette quality, enhanced mechanical strength, and minimal energy consumption. Our knowledge enables us to fine-tune the process to meet both technical performance and cost-efficiency goals, reducing operational risks and accelerating ROI.
- Roller Presses.
- Extruders.
- Vibropresses.
- Pellet Mills.
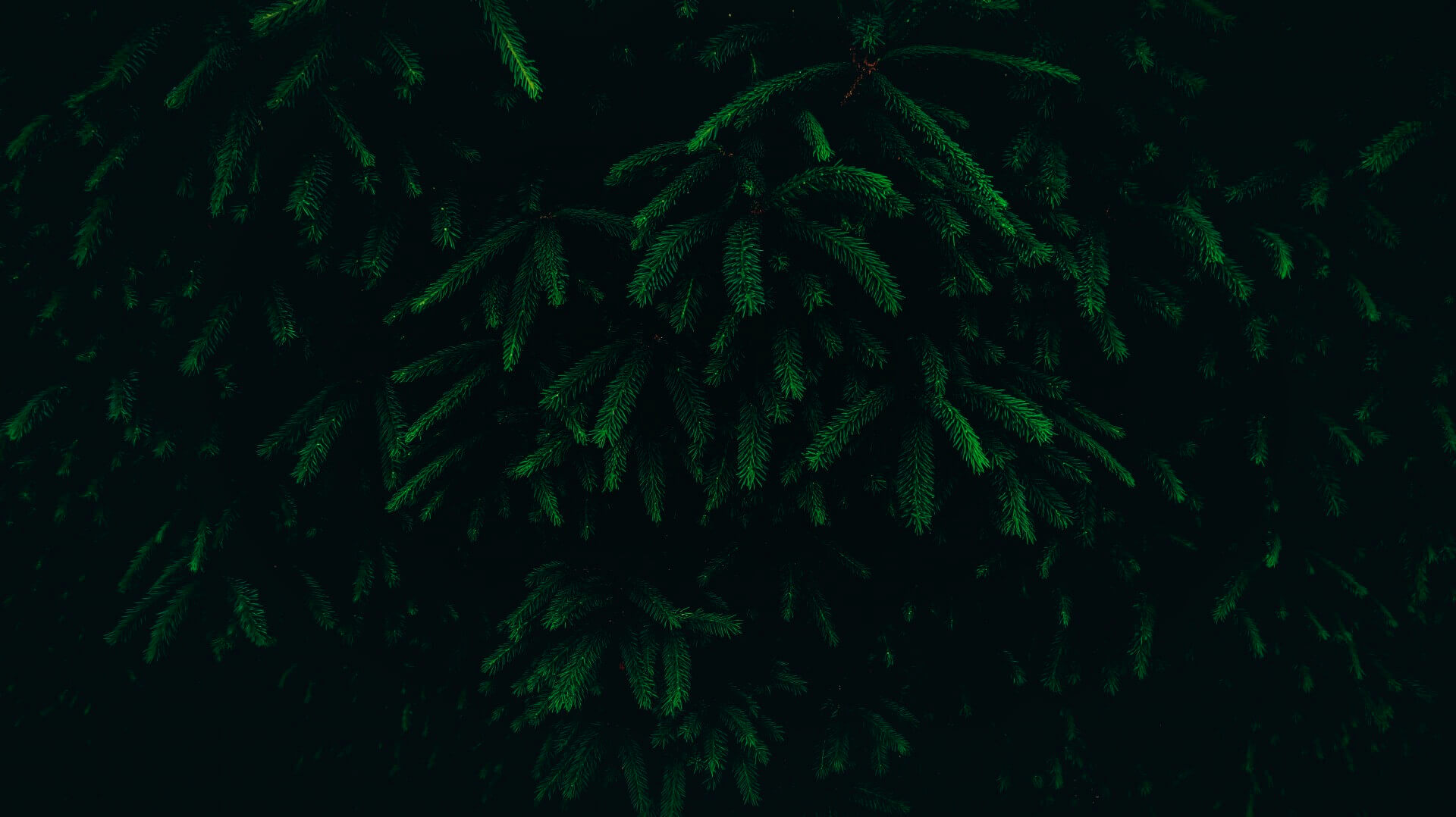
Sectors
Steel Wastes

BF & BOF Dust & Sludge, EAF Dust, Iron Ore Fines, Coke Breeze, Coke Fines, Mill Scale, Scrap Fines & Turnings, Ladle Fines...
By-products from ironmaking and steelmaking operations that contain ferrous and/or carbonaceous content, suitable for recycling into the production loop. These materials are often underutilized due to variability, fine particle size, or contamination but can be transformed into high-value feedstock through cold agglomeration.
How can Cold Agglomeration benefit your business?
- Uniform pellet shape and consistent quality, enabling easier handling and process integration.
- Superior mechanical strength with enhanced binder interaction—boosting CCS, Tumble, and RDI performance.
- Increased durability during transport, storage, and furnace charging.
- Lower energy consumption compared to sintering, with no need for high-temperature curing.
- Reduced emissions and landfill diversion, improving waste valorization and ESG performance.
- Supports circularity goals by reintegrating metallurgical waste into the value chain.
Primary Ores

Concentrates and Direct Shipping Ores from various origins
Iron Ore (Magnetite, Hematite, Goethite...), Manganese Ore, Magnesium Ore, Chrome Ore, Nickel Ore, Pyrite, Spodumene, Bauxite, Quicklime, Slaked Lime...
Ores that are typically processed into pellets or sinter but can be agglomerated cold to reduce emissions, cut capital and operating costs, and enable decentralized processing near the mine or user.
How can Cold Agglomeration benefit your business?
- Comparable performance to indurated pellets in terms of strength and reducibility, without the sintering step.
- Compatible with ore blends, fluxes, and reductants, allowing recipe flexibility and feedstock optimization.
- >80% GHG reduction vs. conventional pelletizing routes, aligning with carbon neutrality targets.
- Greater density and strength, ensuring optimal furnace performance and reduced degradation.
- Lower CAPEX and OPEX due to ambient temperature processing and simplified equipment setup.
- Supports decentralization of agglomeration, ideal for remote or modular mining operations.
Mineral Coals

Coking Coal, Petroleum Coke, Anthracite, Bituminous Coal, Subbituminous Coal, Lignite, Peat...
Fine coal by-products from beneficiation plants, crushing, or storage systems, often discarded or sold at discounted prices. These carbonaceous materials retain high calorific value but suffer from poor flowability and dust generation. Agglomeration unlocks their use in energy-intensive industries with tailored combustion properties.
How can Cold Agglomeration benefit your business?
- Improved fuel performance through enhanced calorific value and combustion uniformity.
- Dust suppression and improved flowability, reducing handling hazards and losses.
- Customizable blends to meet specific energy or metallurgical profiles.
- Potential cost savings by upgrading low-value fines into usable feedstock.
- Facilitates cleaner coal use with reduced particulate emissions and better furnace control.
Biochar & Biocarbon (Biogenic Coals)

Torrefied Biomass, Charcoal, Carbonized Organic Waste...
Biogenic carbon materials derived from forestry, agriculture, or sewage sludge, either raw or thermochemically treated (e.g., torrefied or pyrolyzed). These residues are increasingly sought as carbon-neutral reductants or fuels but require densification and stabilization to match industrial handling and combustion standards.
How can Cold Agglomeration benefit your business?
- Enables use of biogenic waste streams (e.g. biomass) for sustainable heat and reductant applications.
- Reduces spontaneous combustion risks, enhancing storage safety.
- Production of high-quality pellets with uniform density, calorific content, and moisture control.
- Supports circular bioeconomy, substituting fossil carbon in metallurgical and thermal processes.
- Carbon-negative potential, improving overall emissions balance and creating green branding opportunities.
Other Wastes

Mine Tailings, Red Mud, Fly Ash, Black Mass, Slag, Construction Debris, Rubble...
Industrial by-products and mineral residues not traditionally reused in metallurgical processes due to high gangue content, poor physical properties, high moisture, or environmental risk. These include tailings, red mud, fly ash, and other chemically complex wastes, which can be transformed into stable, valuable products through agglomeration and conditioning.
How can Cold Agglomeration benefit your business?
- Converts liabilities into value-added products, contributing to zero-waste objectives.
- Improved handling and transport through dust-free, shaped agglomerates.
- Stabilization and immobilization of harmful components, reducing leachability and environmental risk.
- Enables reuse in construction, cement, or filler markets, opening new revenue streams with the introduction of new building materials and co-products.
- Supports site rehabilitation and CSR initiatives, especially for legacy waste management.
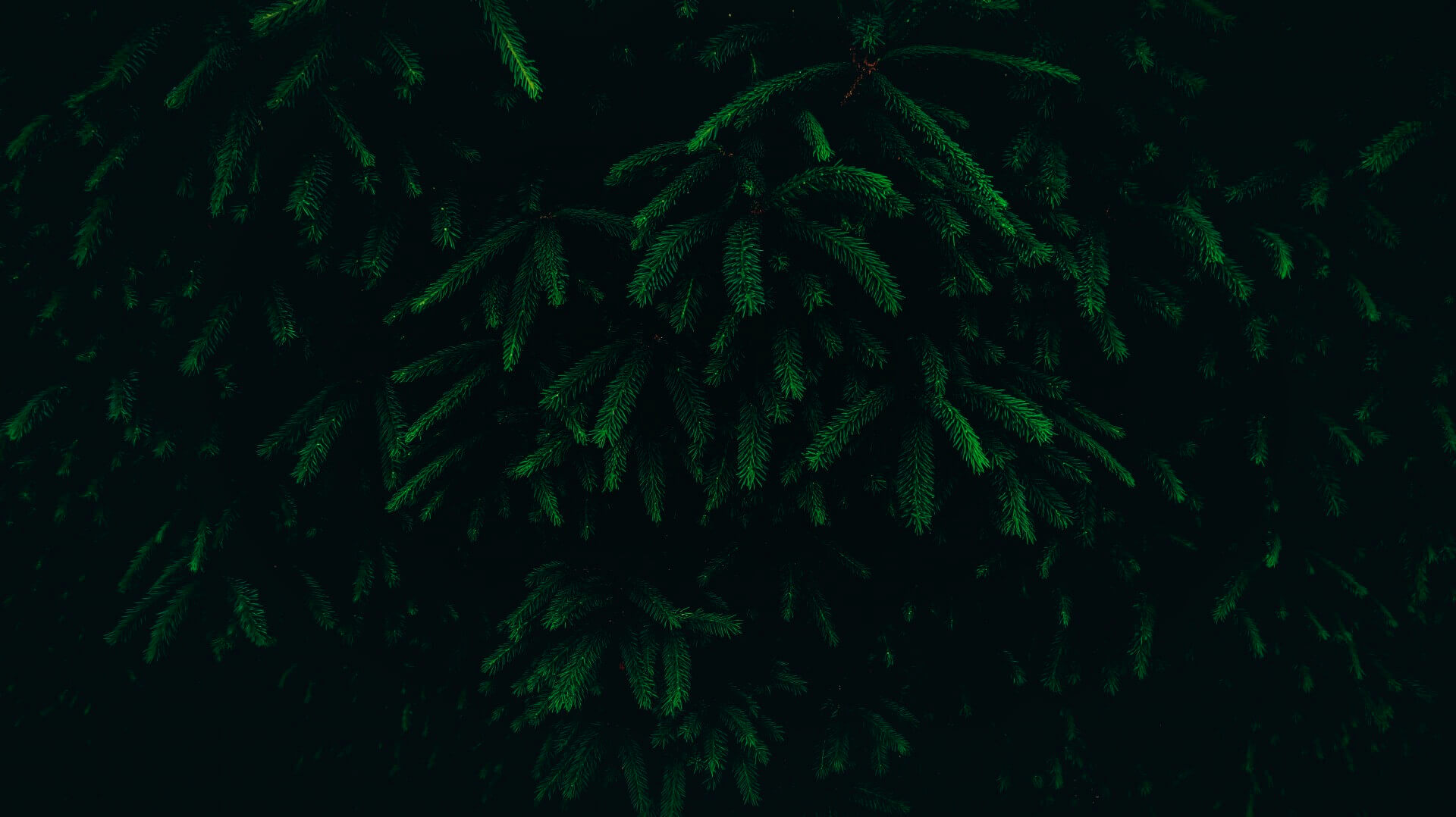
Case Studies

---
NA
---

---
NA
---

---
NA
---
FAQs
1. How can Coldbound Technologies support my decarbonization goals?
Coldbound Technologies offers an innovative portfolio of cold agglomeration recipes and technologies that integrated represent a fast and reliable method to swiftly decarbonize the agglomeration step. Phasing out from sintered and indurated product has never been this simple.
2. How does this differ from the current OEMs offering?
Coldbound Technologies provides a comprehensive assessment and integrated process that identifies the Best Available Technologies for each product of your interest. We always keep profitability and productivity in mind, instead of promoting a specific process.
3. ---
---
4. ---
---
5. ---
---